Facts and figures
Technical data for submerged arc longitudinal and circumferential seam welding systems
Outer diameter: | 406,4 – 12.000 mm | 16″ – 472,4″ |
---|---|---|
Wall thickness: | 6 – 150 mm | |
Lengths: | 1.500 – 28.000 mm |
Welding speeds: | 300 – 2.400 mm/min. |
---|---|
Materials: | all weldable carbon and stainless steels |
Submerged arc longitudinal and circumferential seam welding systems (inside/outside)
Submerged arc longitudinal and circumferential seam welding systems from AWS Schäfer offer you maximum flexibility and efficiency thanks to their stationary or mobile design and the use of 1 to 5-wire welding technology.
- Welding head with linear supports, wire feed unit with servo drive technology
- Camera system, non-contact or tactile height and side scanning
- Innovative wire guide and wire straightening unit
- Energy-saving inverter technology
- AWS ONE Master Control process control system based on Siemens S7 with complete control panel for all system functions including control of workpiece manipulation
- Welding data monitoring system
- Remote maintenance module for uncomplicated and fast problem solving
- Heated welding flux supply system with flux recovery
Submerged arc plate welding system
The submerged arc plate welding systems from AWS Schäfer can be used to produce steel plates that are not available in conventional sizes. These welded plates are used in the manufacture of pipe sections for offshore foundations and for composite panels in shipbuilding.
- Stationary version rotatable by +/-180° or as a mobile portal
- Sheet support tables with integrated sheet manipulation device
- Optional 1- to 5-wire submerged arc welding technology
- Welding head with linear supports, wire feed unit with servo drive technology
- Camera system, non-contact or tactile height and side scanning
- Innovative wire guide and wire straightening unit
- Energy-saving inverter technology
- AWS ONE Master Control process control system based on Siemens S7 with complete control panel for all system functions including control of workpiece manipulation
- Welding data monitoring system
- Remote maintenance module for uncomplicated and fast problem solving
- Heated welding flux supply system with flux recovery
Submerged arc welding column and boom
Our submerged arc welding machine carriers enable precise welding of longitudinal and circumferential seams from both the inside and outside - in a single operation. With smooth operation and the flexible configuration for 1-wire, tandem or 3-wire submerged arc welding technology, they guarantee stability even under extreme conditions. Thanks to the wear-free roller guide system, a long service life and maximum efficiency are guaranteed, even in three-shift operation.
- Designed according to your individual requirements
- Available with 1- to 3-wire submerged arc welding technology
- Servo drive technology in wear-free design
- Camera system, non-contact or tactile height and side scanning
- Innovative wire guide and wire straightening unitEnergy-saving inverter technology
- AWS ONE Master Control process control system based on Siemens S7 with complete control panel for all system functions, including control of workpiece manipulation
- Welding data monitoring system
- Remote maintenance module for uncomplicated and fast problem solving
- Heated welding flux supply system with flux recovery
- Robust, jolt and vibration-reduced design
AWS ONE Master Control - welding and system control unit
The heart of our submerged arc welding systems is the AWS ONE Master Control, which controls all functions and peripherals in a single, user-friendly unit. With interfaces such as Profibus and Profinet, up to five welding wires can be monitored and adjusted simultaneously, while our “Welding Data Analyzer” documents the welding quality in real time.
- Digital process control with auto-tuning and comprehensive system monitoring
- User-friendly interface and visualization of all welding parameters
- Live data monitoring and automatic report generation in the event of deviations
- Job memory function for individual parameter sets and archiving
- RFID operator management with reporting
Submerged arc welding
Sascha Cuntz
Would you like to find out more about our submerged arc welding technology and our services in the areas of submerged arc longitudinal/rotary seam welding systems, submerged arc plate welding systems and submerged arc welding machine carriers? I will be happy to help you!
Sascha Cuntz, your AWS specialist for submerged arc welding
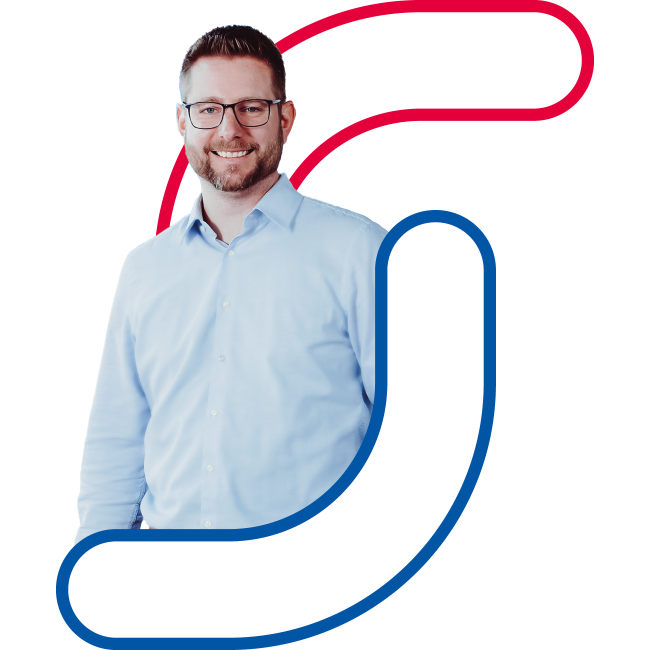
Spitfire
Kristian Völkel
Would you like to find out more about our Spitfire submerged arc welding technology? I will be happy to help you!
Kristian Völkel, your AWS specialist for Spitfire
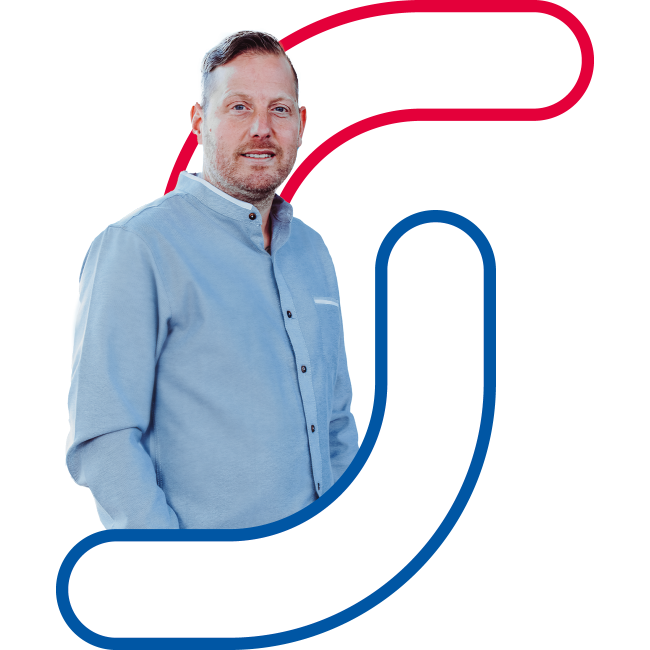
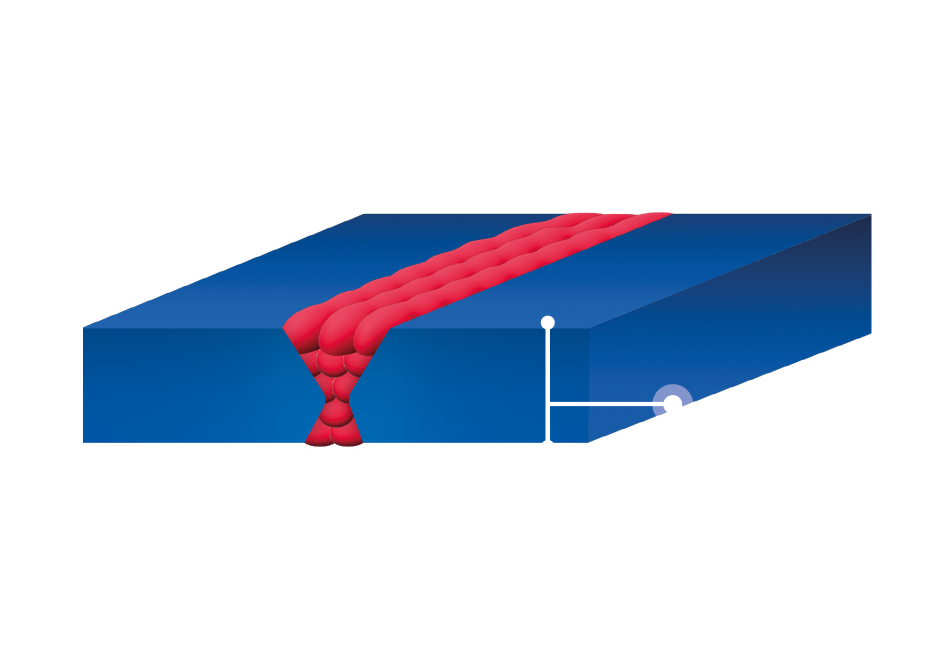
Advantages
- Customized solutions with innovative technology
- System control via a complete control panel
- Low-maintenance and maintenance-friendly system technology
- Integration of all well-known welding power source manufacturers
- High deposition rates with up to five wires
- User-friendly and tried-and-tested user interface
- Welding data monitoring system
- Remote maintenance module for fast support
- Heated welding flux supply system with flux recovery and flux preparation
- Experience as the exclusive supplier of submerged arc welding technology in many pipe mills worldwide
Get to know AWS Schäfer
What is AWS?
AWS Schäfer is an international company based in Siegen for special purpose machines for manufacturing and processing of pipes. Designed and made in Germany, we work for different sectors such as pipeline construction, power plant construction and offshore wind industry.
Discovering new things in the industry with passion and driving innovative ideas forward - that's why we are now known as the Pipe Technologists. Get to know us!
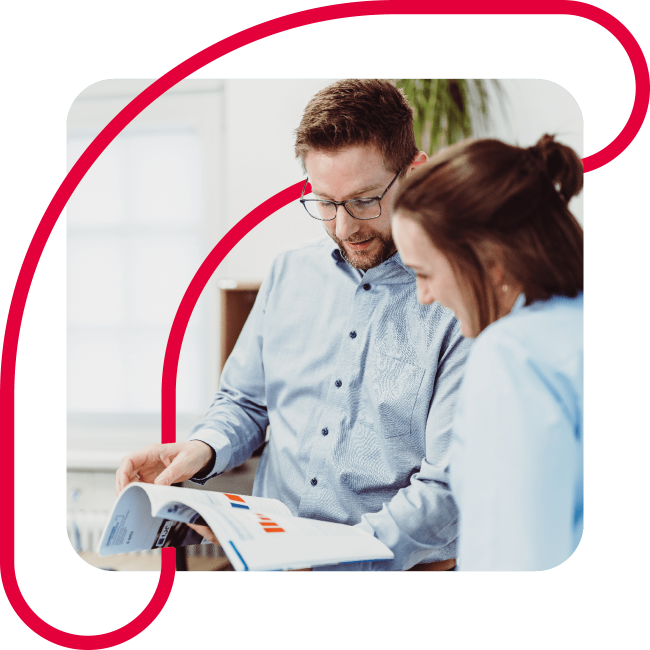
Our quality promise
The AWS principle
Meeting individual requirements
Your requirements are unique. We work with you to develop a machine that is precisely tailored to your needs. We meet your requirements with tailor-made concepts.
Using knowledge successfully
Take advantage of our knowledge! Thanks to many years of experience and our technical expertise in global pipe production, we take all relevant country-specific standards and guidelines into account when developing your machine.
Support at all levels
We are also at your side after your machine has been manufactured. Whether it's on-site assembly, training your employees or adapting to new requirements - we provide you with reliable, long-term support.
Spitfire technology
The Spitfire technology from AWS Schäfer revolutionizes submerged arc welding (SAW) technology with innovative wire preheating. Your advantage? This world's first and new process significantly increases the deposition rate without the need for additional wires on the welding head. This saves you both time and materials. Spitfire technology gives you more precise and efficient weld seams, meets the ever-increasing demands of the industry and offers you both economic and ecological benefits.
Induction bending technology
Induction bending technology from AWS Schäfer offers you precise and efficient bending of pipes, T-beams and profiles, ideal for the petrochemical, oil and gas sectors as well as power plant construction. Our machines enable you to make precise bends with minimal wall thickness reduction and high dimensional stability. Our patented technologies ensure efficient and user-friendly handling, while integrated systems ensure precise geometries and increased product quality. You benefit from reduced costs and increased efficiency.
Hydroforming technology
AWS Schäfer's hydroforming technology is ideal for the production of complex components such as T-fittings and bends in the oil and gas sector. A pipe is precisely formed in a hydraulic press using a liquid medium. The process enables the use of different materials and wall thicknesses in the same tool and offers maximum dimensional and repeat accuracy. Shorter process steps. Low energy consumption. Short cycle times. Hydroforming offers you economy and efficiency throughout the entire production process!
Clad pipe technology
AWS Schäfer's clad pipe technology offers you a cost-effective solution for pipes that have to withstand extreme corrosive conditions in the oil and gas industry. Hydromechanical cladding firmly bonds a corrosion-resistant liner and a carbon steel pipe using high-pressure fluid. This technology enables flexible material combinations, such as ferritic and austenitic steels, as well as aluminum or titanium as liners. The clad pipes produced on our machines offer high corrosion resistance and precise dimensional tolerances, combined with low susceptibility to defects and low investment costs.
Submerged arc welding (SAW)
The submerged arc welding systems (SAW) from AWS Schäfer offer you maximum efficiency and quality when welding long seams! Our systems can be configured flexibly with up to five welding heads and energy-saving inverter technology. You benefit from a user-friendly control system that integrates all common welding power sources and an innovative welding powder supply system that focuses on sustainability and high powder quality. These tailor-made solutions improve your productivity and reduce your operating costs at the same time.
Pipes and pipe mill technology
Whether sheet metal measuring system, sheet metal bending press, pipe calibrating press or pipe end milling machine - our pipe mill technology solutions offer maximum precision and reliability for your demanding pipe production projects! Our modern sheet metal measuring and forming systems as well as end processing machines are in use worldwide and can be seamlessly integrated into existing or newly planned pipe mills.
Special-purpose machines
If standard machines do not meet your requirements, our custom-made machines come into play! Our team of engineers can look back on numerous successful projects in the implementation of individual machines for forming and processing steel and pipe products. We also carry out retrofits, upgrades and conversions of machines and systems.